Ball grid array rework is one of the most challenging procedures performed at assembly facilities and repair depots around the world. Properly acting depends to a large extent on the skills and knowledge of the rework technician. The BGA rework procedure is clear and has been established for a long time, but there are 4 common mistakes. Let's look at the 4 Most Common Mistakes in BGA Rework and how to avoid them!
Related article:
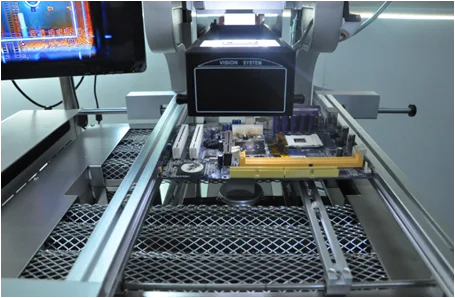
image source: Alibaba
1. Insufficient operator training
BGA rework technicians must be fully trained to master their skills. They must understand the materials, tools, process steps, and the interrelationships of all the factors they use.
Before starting to rework, they must have the skills to assess and “determine” BGA rework in terms of knowledge and skill. And they must be able to identify subtle, persuasive signs that indicate the process is off-track.
2. Inappropriate equipment selection
You need the right tools to work properly. For BGA rework, the equipment used must be sophisticated, flexible, and capable of maintaining a controlled, predictable, and repeatable process.
This includes closed-loop thermal sensing and control, the robustness to be able to deliver heat for process requirements, and product handling capabilities for disassembly and replacement. Use the most powerful device, this is not a place to cut corners.
3. Collateral thermal damage
Reflow of soldered connections of adjacent components results in oxidation, de-wetting, damage to pads and leads, wicking, lack of joints, component damage, and other issues that can create many new rework problems.
Technicians must constantly understand the impact of heat on the target BGA device and how it affects other components on the sides of the component that are adjacent to it. The goal is to minimize heat transfer beyond the reworked BGA assembly, which is a sophisticated profile and rigorous process control.
4. Insufficient Post-Placement Inspection
The world beneath a BGA component is a hidden mysterious place, but not from today's X-ray inspection machines. Problems such as excessive voiding and poor placement or alignment are immediately detectable with X-ray inspection.
But just like a Radar operator, an X-ray system user needs proper training to correctly interpret and understand the image that the machine is providing. The complexity of the BGA component and the different variations in the X-ray image demands it if maximum benefit is to be obtained from this significant - and indispensable - equipment investment.
Avoiding the 4 Most Common Mistakes in BGA Rework is the best way to ensure a successful, robust, and repeatable process with fewer headaches, higher yields, and reduced costs for a better bottom line.
The world beneath a BGA component is a hidden mysterious place, but not from today's X-ray inspection machines. Problems such as excessive voiding and poor placement or alignment are immediately detectable with X-ray inspection.
But just like a Radar operator, an X-ray system user needs proper training to correctly interpret and understand the image that the machine is providing. The complexity of the BGA component and the different variations in the X-ray image demands it if maximum benefit is to be obtained from this significant - and indispensable - equipment investment.
Avoiding the 4 Most Common Mistakes in BGA Rework is the best way to ensure a successful, robust, and repeatable process with fewer headaches, higher yields, and reduced costs for a better bottom line.
Related article:
Comments
Post a Comment