The surface mount segments is small and can be mounted on either side of the PCB and adds extensive use of hardware. The advantages of SMT or surface mount technology can be used in both design and development.
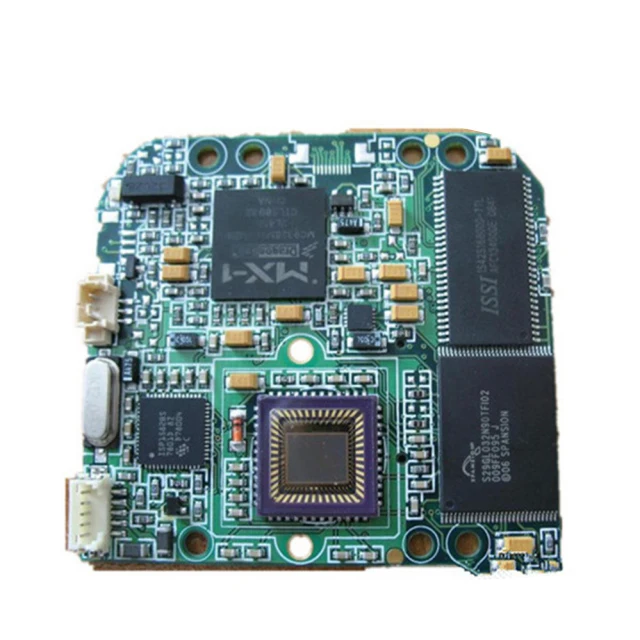
image source: Alibaba
Advantages of surface mount technology in design
The most important benefit of the Design section is that it can significantly reduce weight and electrical noise.
The weight of the SMT component is only one-tenth of the normal thru-hole equivalents. For this reason, the weight of the surface mount component (SMA) is significantly reduced.
SMT components occupy little space because this is only half to one-third of the printed circuit board space.
Since each electronic component is not accessible in surface mount, the real area reserves on a board will depend on the ratio of through-hole components changed by surface mount parts.
Advantages of surface mount technology in manufacturing
Important advantages of SMT in manufacturing include reduced board cost, reduced material handling costs, and controlled manufacturing processes.
The routing of the traces is reduced, the size of the board is reduced, and the number of drill holes is also reduced.
If the function on the surface mount board is not expanded, the expansion of the inter-package spacing and the reduction in the number of drill gaps achieved by the smaller surface mount components can also reduce the number of layers in the printed circuit board. This will again reduce board costs.
The above advantages of surface mount technology do not necessarily mean that SMT assembly will always reduce costs. It depends on when and how to use SMT.
Disadvantages of surface mount technology
Small lead space may make maintenance more difficult.
There is no guarantee that the solder connections will withstand the compounds used in the potting application. The connection may or may not be damaged during thermal cycling.
Components that generate a lot of heat or withstand high electrical loads cannot be installed using SMT because the solder may melt at high temperatures.
Solder is also weakened due to mechanical stress. This means that the physical binding of the through-hole installation should be used to connect the components that will interact directly with the user.
Related article:
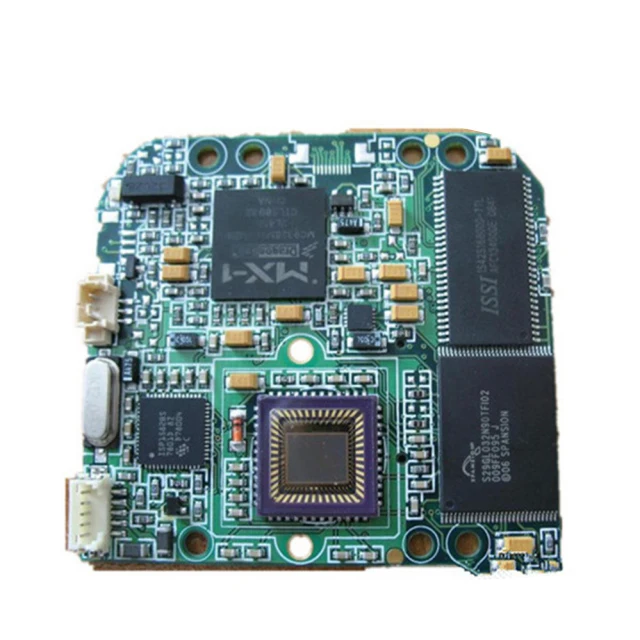
image source: Alibaba
Advantages of surface mount technology in design
The most important benefit of the Design section is that it can significantly reduce weight and electrical noise.
The weight of the SMT component is only one-tenth of the normal thru-hole equivalents. For this reason, the weight of the surface mount component (SMA) is significantly reduced.
SMT components occupy little space because this is only half to one-third of the printed circuit board space.
Since each electronic component is not accessible in surface mount, the real area reserves on a board will depend on the ratio of through-hole components changed by surface mount parts.
Advantages of surface mount technology in manufacturing
Important advantages of SMT in manufacturing include reduced board cost, reduced material handling costs, and controlled manufacturing processes.
The routing of the traces is reduced, the size of the board is reduced, and the number of drill holes is also reduced.
If the function on the surface mount board is not expanded, the expansion of the inter-package spacing and the reduction in the number of drill gaps achieved by the smaller surface mount components can also reduce the number of layers in the printed circuit board. This will again reduce board costs.
The above advantages of surface mount technology do not necessarily mean that SMT assembly will always reduce costs. It depends on when and how to use SMT.
Disadvantages of surface mount technology
Small lead space may make maintenance more difficult.
There is no guarantee that the solder connections will withstand the compounds used in the potting application. The connection may or may not be damaged during thermal cycling.
Components that generate a lot of heat or withstand high electrical loads cannot be installed using SMT because the solder may melt at high temperatures.
Solder is also weakened due to mechanical stress. This means that the physical binding of the through-hole installation should be used to connect the components that will interact directly with the user.
Related article:
Comments
Post a Comment